“Kezurou-kai” is Japanese group with 15,000 members. Translation of this name to English means “Shaving – group” demonstrate the traditional Japanese hand tools, techniques and traditional method of building such as post and beam and stucco wall finish to the public. As people know, Japanese blade are made out of melting carbon steel to soft steel so it is hard and sharp at the carbon edge but flexible so shape can be adjusted, all done by hand except the pounding to strengthen the steel has some machine hammer on duty. This include swords, knifes, chisels and planer blades. Why does this matter? It only matters for people does real fine work and people push the limits, craftsman and artist entire world, when they meet these fine Japanese tools that are made with skills, they fall in love because it does bring the work to the next level.
Hand planing is great example. Hand planer mainly used for two different application shaping the wood or finishing the surface, in joinery work it makes flat surface and shave the wood to line, shaving to pencil line but to outer edge of line or center of line depends on character of joinery, this is the scale of 1/32 inch as pencil line and joinery size to be control by 1/64 inch. For finishing if wood is planed properly, it gives mirror finish that would shed water which means stain would not penetrate in, this is the finish applied for the temples and still many Japanese style house build today. No stain!
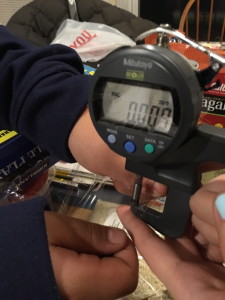
saran wrap measures 9 micron at house
What happen if those professionals competing how thin it can be planed? This competition is about pushing limit, rules are plane shavings to be full width and full length and measure 3 points and take the thickest point not the thinnest point. Measuring instruments are micrometer. Micrometer measure the thickness in micron. 1 Micron is 1/1000 of millimeter or 0.00004 inch. 20lbs paper is a bit over 100 micron, saran wrap may be the one of thinnest material we touch often which is about 7-9 micron I measured at my house.
Long story short, winners at the Japanese competitions are around 4 micron, record I heard are 1 or 2 micron but not official. This is totally crazy, it does not change the dimension of wood, it takes 250 times of this shaving to lose 1mm in a wood.
First try at our shop 4 weeks prior to competition, with same way we have been sharpening, wood surface were nice and shining after plane, I did not had micrometer so I asked Kazu “What you think this shaving thickness is?”, He is the only one has attend the event in Japan but never competed and he told me “My guess would be around 40 micron” . I had no clue what that means but I thought it should be better than that, so order the micrometer and a few sharpening stone from Japan.
From this date, we had 4 weeks to competition and we hooked into this, plane the wood after work every day, we occupied the bathroom at the house every single night (Bath room has different use for Japanese wood worker, it is sharpening room), too embarrassed to even mention how long each night were to spend on this. My wife try not to spoke about, only my son Taro comes in bath room once every night and he say to me “One day off, puts three days back, right?” I said to my son “You know it, that is why I even took this to our year end camping last weekend!”
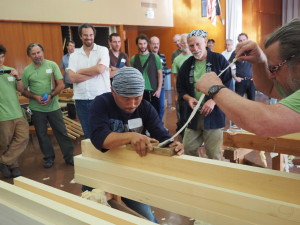
Kiyo got thinnest 5 micron
Story would not end, and for the people want to take off here, here is the result. 25-27 people enter into competition, we are only Canadian crossed border to join the event, thinnest shaving was 5 micron but it was not full width and length. Qualified shavings I thought were a few 7-9 micron and a few 10-16 micron. Kiyo was the one got 5 micron, Kazu had 10 micron full width, full length, consistent, Eijiro got good 16 micron, we all had our best at the competition so Daizen team did very well. I unfortunately got late to the competition, spend too much time on socializing…. It would been around 10-12 micron, will revenge next year!

Kazu, first try, 20 micron, he got 10 micron after this try
Here continue the story.
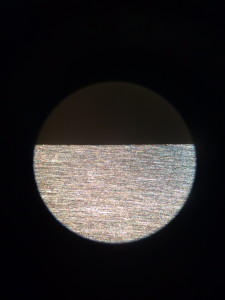
zoomed with x20 microscope, I have been using this microscope for about 20 years and edge looks good, it is very sharp. This is showing finish with 8,000 grid, shows nice and smooth to the edge
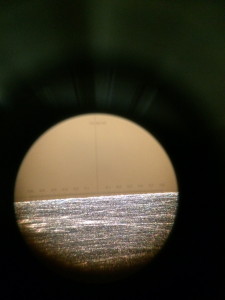
This is picture with X100. Picture is not taken same blade but same principal, back side of planer blade finish with 8,000 grid. This shows the edge is not reached with sharpening and some large scratch. From this, I figure water at my house contains calcium that effecting this scare, since I saw this, I use only pure water prior to 8,000 grid. So it looks great in X20 but not in X100 which gave me some ideas how I can improve.
Chesel and planer blade sharpening, what matters most is the back side of the blade. How to sharpen this flat matters. In planing, if the back is sharpened properly, there are guy says he gets 10 micron with 1,000 grid sharpening at front edge. This is true. Chesel and planer both has hollow back which is to make the flat sharpening easier and more perfectly. This hollow is made prior the forge so it is not something would work same such as gliding the back hollow. For the planer, focus is to leave the sharpening surface minimum, if you keep sharpening the back, it makes flat wider and wider, instead, we pound the soft steel at front to push the blade so keep the flat surface minimum.
Water at my house, contains calcium, if I boil water in kettle for tea, it is visually notice, I see some white settlement, this definitely cause the sharpening so I made sure to clean the blade and stone and only use the filtered water prior to finish.
I used to use only 800 grid then prior to finish. This was enough to maintain very sharp edge for chisel and normal work but to go for 10 micron and less, I needed to stone, I purchased, #1,000, #2,000 and natural finishing stone (equilibrant to #8,000) and eliminate using #800.
Sharpening is moving from one grid to others, coarser to finer. At each stage, it create burbe at the edge and how much it creates is the measurement to move into next grid. Though rough grid such as #800 seems like damage the edge too rough it makes the edge week.
Difference between natural #8,000 grid and natural stone is that natural stone create aggregate that become finer and finer as kept sharpening but more the less, placing this in between the blade and stone, it works like compound that maintain the flat of the stone better. These are really hard to understand that you need to put time into this to feel.
So, 4 hours of sharpening every night was to explore, set the theory, and gain more skills of sharpening. Actual sharpening, maintaining edge from not damaged blade is about 30 min max.
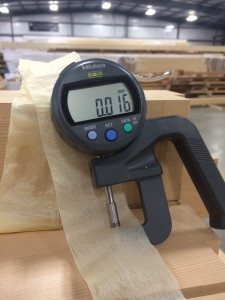
One week prior to competition, my best was 16 micron. All hope was to wait the set of new stone that ordered but have not came in. New set of stone contains #8,000 diamond stone I meant to use only for the back side of planer blade so it reach to the edge with flat and also finish so none of other wrapping is needed.
Driving to Santa Clara was 20 hours drive.
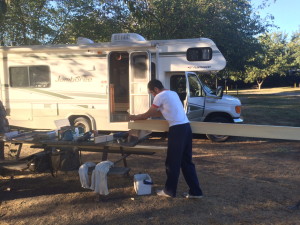
Planing wood at KOA campsite California 30 min after parked.
Event was Saturday so we left Kamloops after the work, Thursday 4PM. 4 of us got into my motorhome and started driving, felt like teens that something exciting ahead waiting for us. Long way ahead so I thought I would not talk about planer blade, base maintenance and so on, but conversation started right after we left and carried all the way to California. Friday 3PM we got close so we camped. All 4 of us brought sharpening set out, try out planing and got back to sharpening. My set of stone came in Wed afternoon and I did not had chance to try yet, so we tried at camp site. Got into dark so we moved to toilet facility at camp site and continue sharpened. Good that it was end of October, not many people at camp site, but a few people around did not even come close us to ask what we were doing, we all had sharp knife on hand and kept sharpening, it must been look so wired.
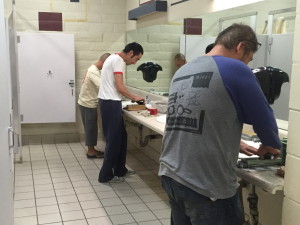
Lucky that bathroom at campsite had 4 sets of sink and nice and bright.
There were lots of great moments but I got right in a activity this time and had not taken any pictures.
Hand planing is very fun and shows how humans are capable that I don’t think machine can compete at the moment. It has lots to it, I only introduced one side of sharpening, how to maintain stone flat, method of sharpening, difference in stone, kind of blade, maintaining the wood base, fine adjustment of base, etc etc.
I am planning to do sharpening workshop at BCLTBI AGM that coming in Feb 19th at Chase Quaaout Lodge, anyone welcome to join.
Read More